Newly Discovered Catalyst Could Lead to the Clean Production of Methanol
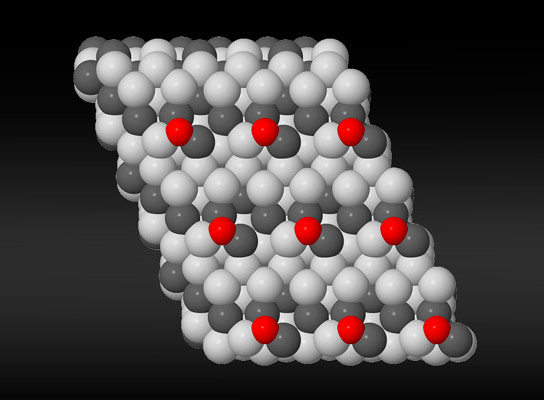
Artist’s
rendering of the nickel-gallium active site, which synthesizes hydrogen
and carbon dioxide into methanol. Nickel atoms are light grey, gallium
atoms are dark grey, and oxygen atoms are red.
A research team has discovered a potentially clean, low-cost way to convert carbon dioxide into methanol, a key ingredient in the production of plastics, adhesives and solvents, and a promising fuel for transportation.
Scientists from Stanford University, SLAC National Accelerator Laboratory and the Technical University of Denmark combined theory and experimentation to identify a new nickel-gallium catalyst that converts hydrogen and carbon dioxide into methanol with fewer side-products than the conventional catalyst. The results are published in the March 2 online edition of the journal Nature Chemistry.
“Methanol is processed in huge factories at very high pressures using hydrogen, carbon dioxide and carbon monoxide from natural gas,” said study lead author Felix Studt, a staff scientist at SLAC. “We are looking for materials than can make methanol from clean sources, such as sunshine, under low-pressure conditions, while generating low amounts of carbon monoxide.”
The ultimate goal is to develop a large-scale manufacturing process that is nonpolluting and carbon neutral using clean hydrogen, the authors said.
“Imagine if you could synthesize methanol using hydrogen from renewable sources, such as water split by sunlight, and carbon dioxide captured from power plants and other industrial smokestacks,” said co-author Jens Norskov, a professor of chemical engineering at Stanford. “Eventually we would also like to make higher alcohols, such as ethanol and propanol, which, unlike methanol, can be directly added to gasoline today.”
Industrial methanol
Worldwide, about 65 million metric tons of methanol are produced each year for use in the manufacture of paints, polymers, glues and biofuels. In a typical methanol plant, natural gas and water are converted to synthesis gas (syngas), which consists of carbon monoxide, carbon dioxide and hydrogen. The syngas is then converted into methanol in a high-pressure process using a catalyst made of copper, zinc and aluminum.
“We spent a lot of time studying methanol synthesis and the industrial process,” Studt said. “It took us about three years to figure out how the process works and to identify the active sites on the copper-zinc-aluminum catalyst that synthesize methanol.”
Once he and his colleagues understood methanol synthesis at the molecular level, they began the hunt for a new catalyst capable of synthesizing methanol at low pressures using only hydrogen and carbon dioxide. Instead of testing a variety of compounds in the lab, Studt searched for promising catalysts in a massive computerized database that he and co-author Frank Abild-Pedersen developed at SLAC.
“The technique is known as computational materials design,” explained Norskov, the director of the SUNCAT Center for Interface Science and Catalysis at Stanford and SLAC. “You get ideas for new functional materials based entirely on computer calculations. There is no trial-and-error in the lab first. You use your insight and enormous computer power to identify new and interesting materials, which can then be tested experimentally.”
Studt compared the copper-zinc-aluminum catalyst with thousands of other materials in the database. The most promising candidate turned out to be a little-known compound called nickel-gallium.
“Once we got the name of the compound out of the computer, someone still had to test it,” Norskov said. “So we had to have a good experimental partner.”
Norskov turned to a research group at the Technical University of Denmark led by Ib Chorkendorff, a co-author of the research paper. First, the Danish team carried out the task of synthesizing nickel and gallium into a solid catalyst. Then the scientists conducted a series of experiments to see if the new catalyst could actually produce methanol at ordinary room pressure.
The lab tests confirmed that the computer had made the right choice. At high temperatures, nickel-gallium produced more methanol than the conventional copper-zinc-aluminum catalyst, and considerably less of the carbon monoxide byproduct.
“You want to make methanol, not carbon monoxide,” Chorkendorff said. “You also want a catalyst that’s stable and doesn’t decompose. The lab tests showed that nickel-gallium is, in fact, a very stable solid.”
While these results show promise, a great deal of work lies ahead. “We’d like to make the catalyst a little more clean,” Chorkendorff added. “If it contains just a few nanoparticles of pure nickel, the output drops quite a bit, because pure nickel is lousy at synthesizing methanol. In fact, it makes all sorts of chemical byproducts that you don’t want.”
Nickel is relatively abundant, and gallium, although more expensive, is widely used in the electronics industry. This suggests that the new catalyst could eventually be scaled up for industrial use, according to the authors. But to make methanol synthesis a truly carbon-neutral process will require overcoming many additional hurdles, they noted.
Other co-authors of the study are Jens Hummelshoj of SLAC; and Irek Sharafutdinov, Christian Elkjaer and Soren Dahl of the Technical University of Denmark.
The research was supported by the U.S. Department of Energy, the Danish National Research Foundation and the Danish Ministry of Science, Technology and Innovation.
Publication: Felix Studt, et al., “Discovery of a Ni-Ga catalyst for carbon dioxide reduction to methanol,” Nature Chemistry, 2014; doi:10.1038/nchem.1873
Image: Jens Hummelshoj/SLAC
Your Opinion is valid .